Pilar CERALOG® – innovador y fabricado del polímero de alto rendimiento PEKK
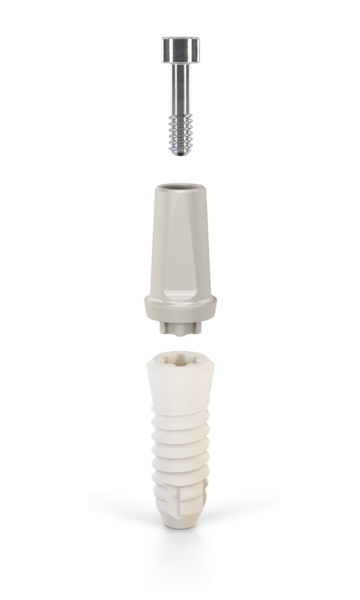
El sistema de implantes CERALOG® incluye pilares rectos y angulados fabricados de polietercetonacetona de alto rendimiento (PEKK). Los pilares se fijan en el implante con un tornillo de titanio o de oro. El PEKK posee un color claro y es fácil de procesar con un set de fresas convencional.
El polímero de alto rendimiento PEKK
PEKK pertenece a la familia de los poliaril éter cetona (PAEK). Son termoplásticos de alto rendimiento necesarios y utilizados en condiciones extremas, por ejemplo, en la industria automovilística, en la industria aeroespacial y en la ingeniería médica. Gracias a su composición química ofrecen una resistencia a la tracción excelente, rigidez y resistencia a la hidrólisis.
Además de su uso prolongado en la ortopedia, el PEKK también cubre un amplio espectro de indicaciones en la odontología. La ductilidad del PEKK reduce el factor de estrés sobre el implante y simula un comportamiento similar al del diente.
Componentes CERALOG®
Componentes CERALOG® para el manejo de los tejidos blandos
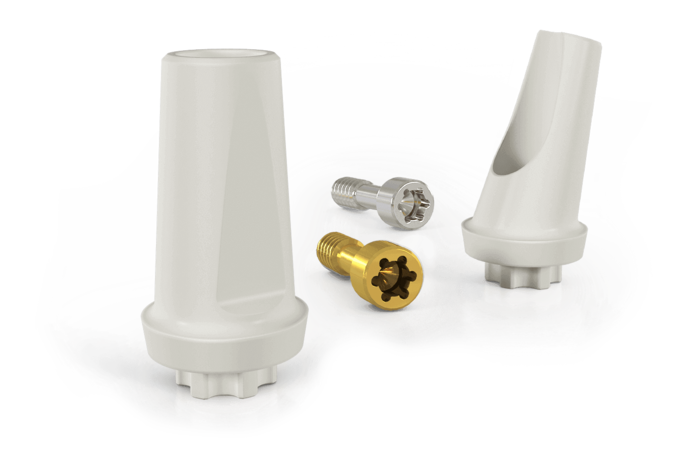
El set del implante CERALOG® Hexalobe incluye un tapón de cierre que se inserta en la conexión Hexalobe durante la cicatrización. Opcionalmente, el implante se puede cubrir con un tornillo de cierre.
Ambos implantes se pueden usar para la cicatrización abierta y sumergida. Para la modelación del tejido blando los tapones de cicatrización están disponibles en dos diámetros, igual que los pilares provisionales. Estos componentes están fabricados de PEEK y se usan durante un tiempo limitado.
Toma de impresión CERALOG®
El uso de una cofia de transferencia o de un poste de transferencia permite tomar las impresiones de los implantes CERALOG® Hexalobe tanto con cubeta abierta como cerrada.
PEEK frente a PEKK
El polímero de alto rendimiento polieteretercetona (PEEK) es el más conocido y se utiliza en la odontología desde hace años para las restauraciones provisionales, el escaneado y los postes de toma de impresión. También pertenece al grupo de polímeros PAEK (poliaril éter cetona). La síntesis del PEKK comenzó en 1962 por el grupo químico DuPont, que ha perfeccionado la polimerización desde entonces.
La posterior síntesis del PEKK fue adaptada por Oxford Performance Materials y Arkema, quienes iniciaron la introducción del material en diferentes segmentos industriales del mercado. La principal ventaja del PEKK frente al PEEK es su mayor resistencia a la fatiga y a la compresión bajo carga de esfuerzo.
PEKK | PEEK | |
---|---|---|
Módulo de Young (GPa) | 4.5 | 4.1 |
Resistencia a la tracción (MPa) | 138 | 100 |
Resistencia a la flexión (MPa) | 193 | 165 |
Resistencia a la compresión (MPa) | 207 | 135 |
Alargamiento de rotura (%) | >30 | 40 |
Temperatura de fusión (°C) | 360 | 340 |
Absorción de agua después de 24 h (%) | <0.2 | 0.5 |
Densidad (g/cm³) | 1.3 | 1.3 |